Extreme Weather Renewable Energy – 150 MPH Ground Mount Solar
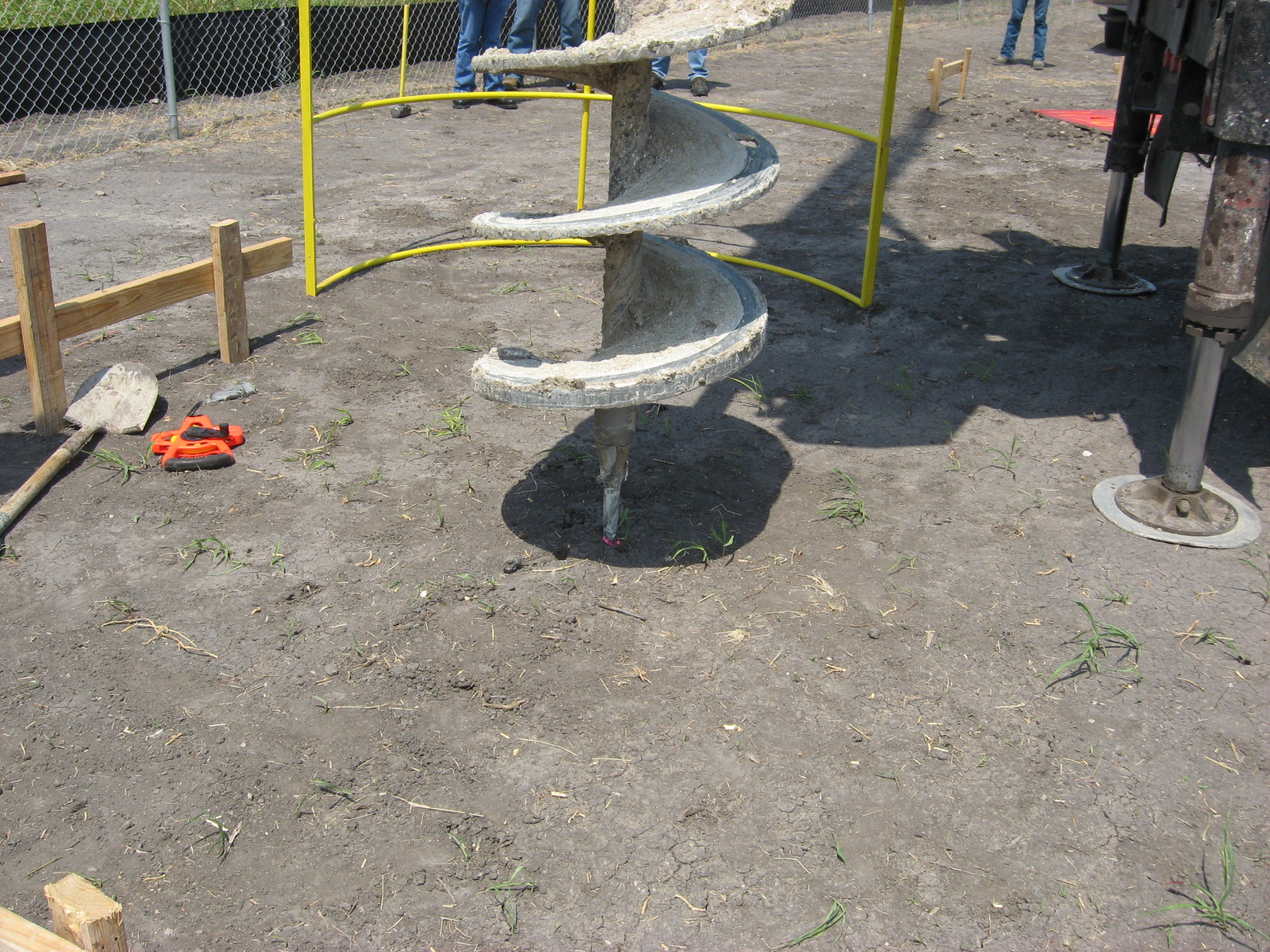
Drilling Solar Array Piers
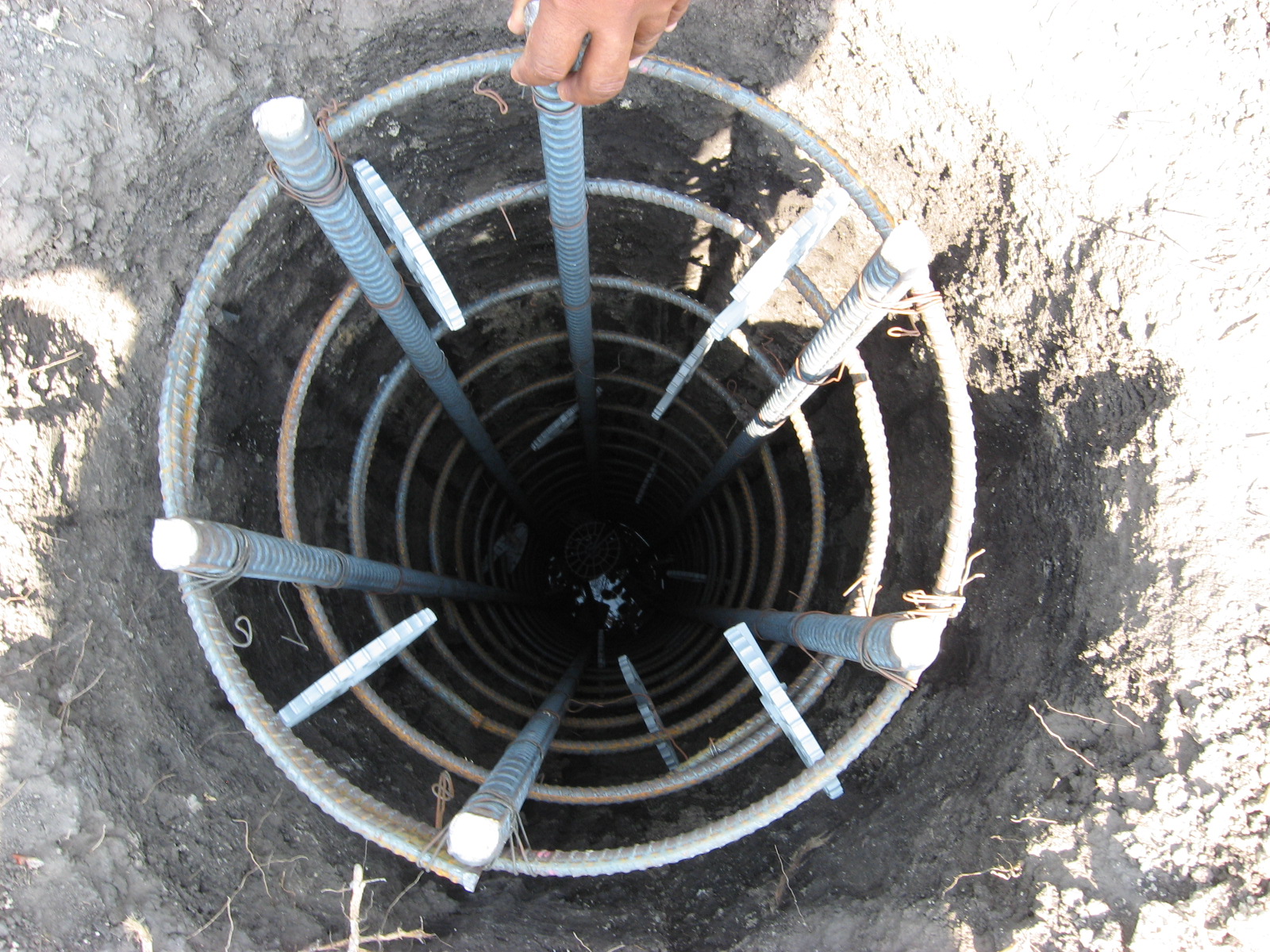
Preparing for Concrete Pour
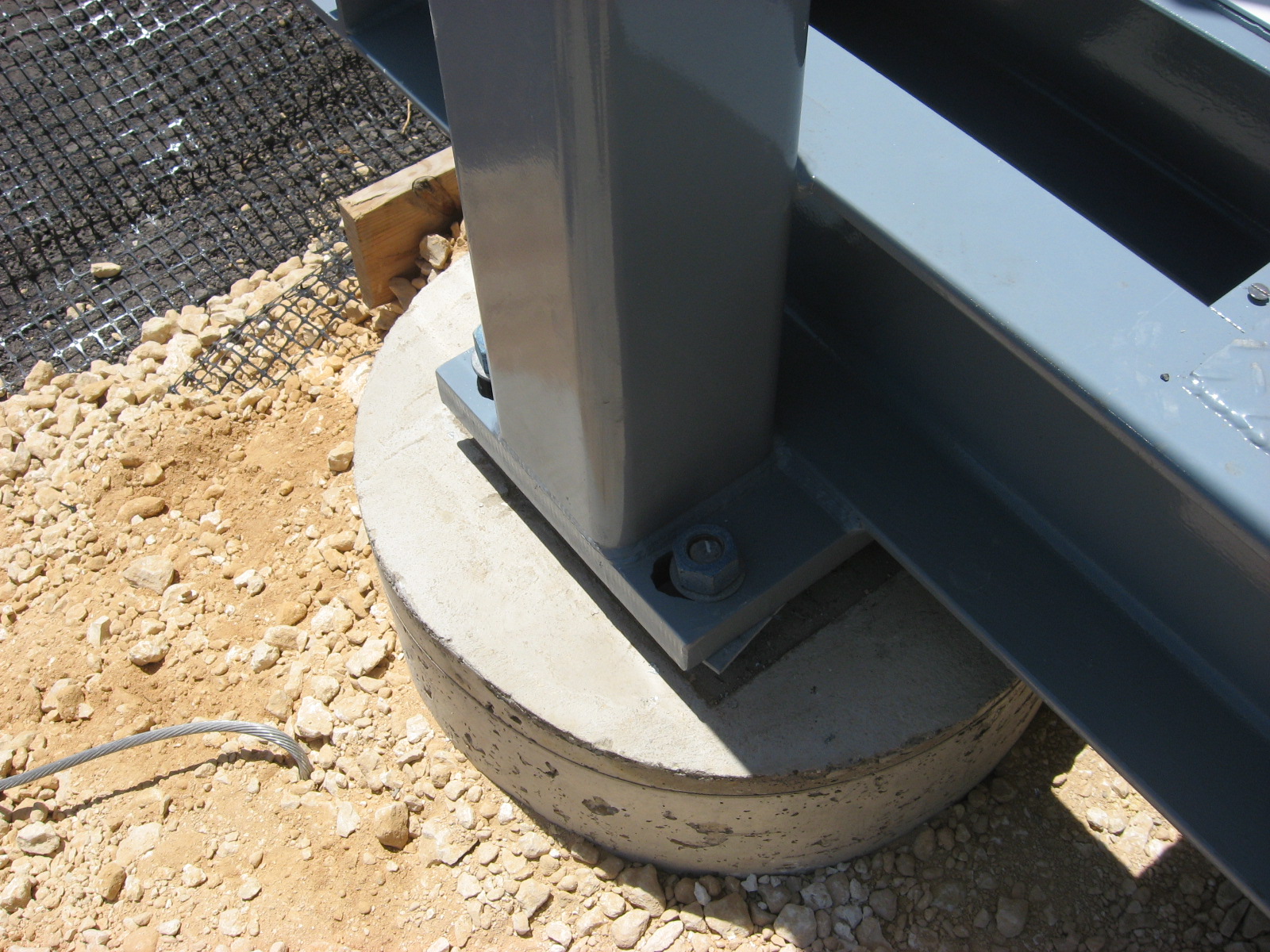
Racking Securely Attached
Many critical Department of Defense (DoD) installations are located in coastal areas that are vulnerable to extreme weather events and constantly exposed to corrosive marine environments. Ensuring a cost-effective extreme weather renewable energy solution that will withstand these effects over a 20-year project lifecycle can be challenging.
Hurricane Exposures
The Naval Air Station (NAS) Kingsville is exposed to some of the worst weather that Mother Nature can dish out, including hurricane force winds that can gust up to 200 miles per hour. Designing a lowest-cost, hurricane tolerant ground mount solar array that was Buy American Act-compliant, required significant due diligence and numerous design iterations. PowerSurety staff, employed by Chevron USA Inc., at the time, worked with solar module manufacturers to develop a component-interlocking design to ensure that exacting wind loads were taken into account so that the system could achieve the requirement of being hurricane tolerant to 150 mph in wind velocity.
DoD Unified Facility Criteria Specification Development
The Kingsville solar PV project was one of the first ground-mount solar PV energy plants built on a DoD site with poor soil conditions that was specifically designed with hurricane tolerance in mind. Another key deliverable was the development of new specifications to supplement the DoD’s Unified Facility Criteria (UFC) and corresponding Guide Specifications (UFGS) that hadn’t yet been updated to include ground-mount solar PV engineering and construction policies and procedures.
Poor Existing Soil Conditions
Wind is traditionally one of the most frequent causes of damage to solar arrays and NAS Kingsville was concerned about having the array be a dependable source of renewable power when required. Both the need to design to a constant 150 MPH coupled with the poor soil characteristics of the site, required extensive design iterations and custom modeling to ensure compatibility.
Wind force of that magnitude causes deflection, both on array components and on the solar panels themselves. Design calculations employed 3-D CAD modeling to aid in running simulations to account for varying wind directions and speeds.
3-D Modeling Enabled Analysis
Various design layouts and racking configurations for the extreme weather renewable energy system produced different wind impact on both panels and structural components. Design iterations included round tubes versus square or other shaped steel to determine the most cost effective means to handle the torsional loads.
Modeling and design iterations were preformed until panels and system components would withstand steady state winds of 150 mph with short term peaks of up to 175 mph.